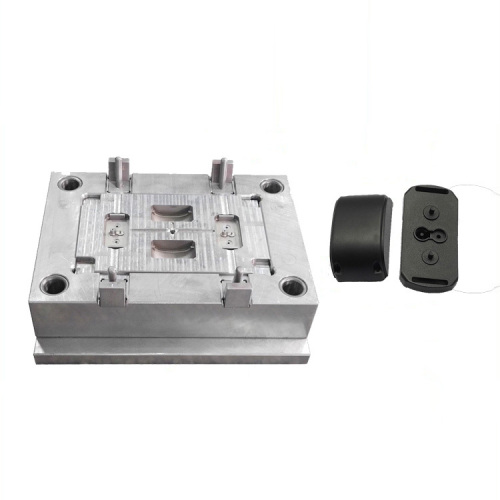
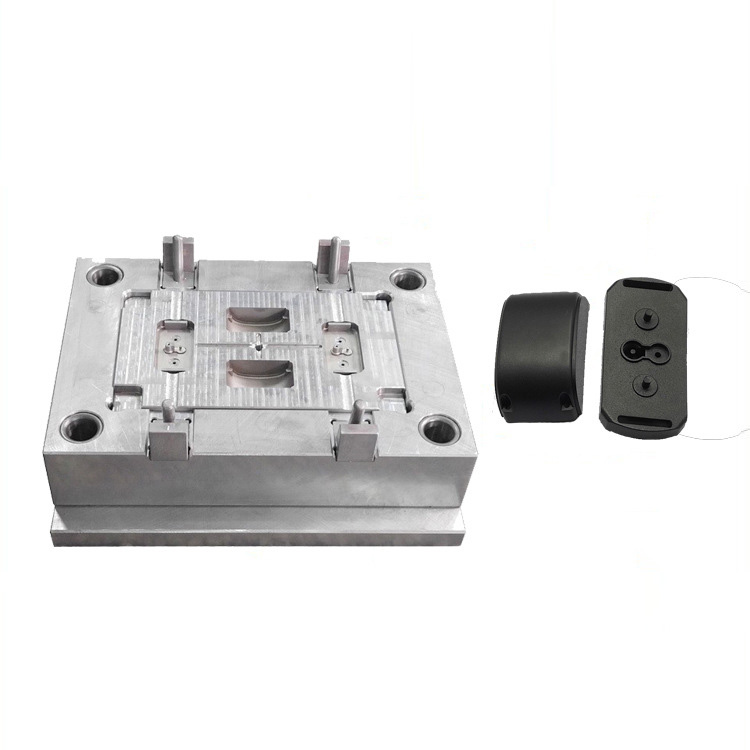
Payment Type:T/T,Paypal
Incoterm:FOB,EXW
Min. Order:1 Piece/Pieces
Transportation:Ocean,Air
$1500≥1Piece/Pieces
Model No.: AD-104
Brand: AD-269
Forming Method: Plastic Injection Mould, Preform Mould, Extrusion Mould
Product Material: Plastic
Transportation: Ocean,Air
Payment Type: T/T,Paypal
Incoterm: FOB,EXW